How to Select the Perfect Heat Exchanger for Your Industrial Application
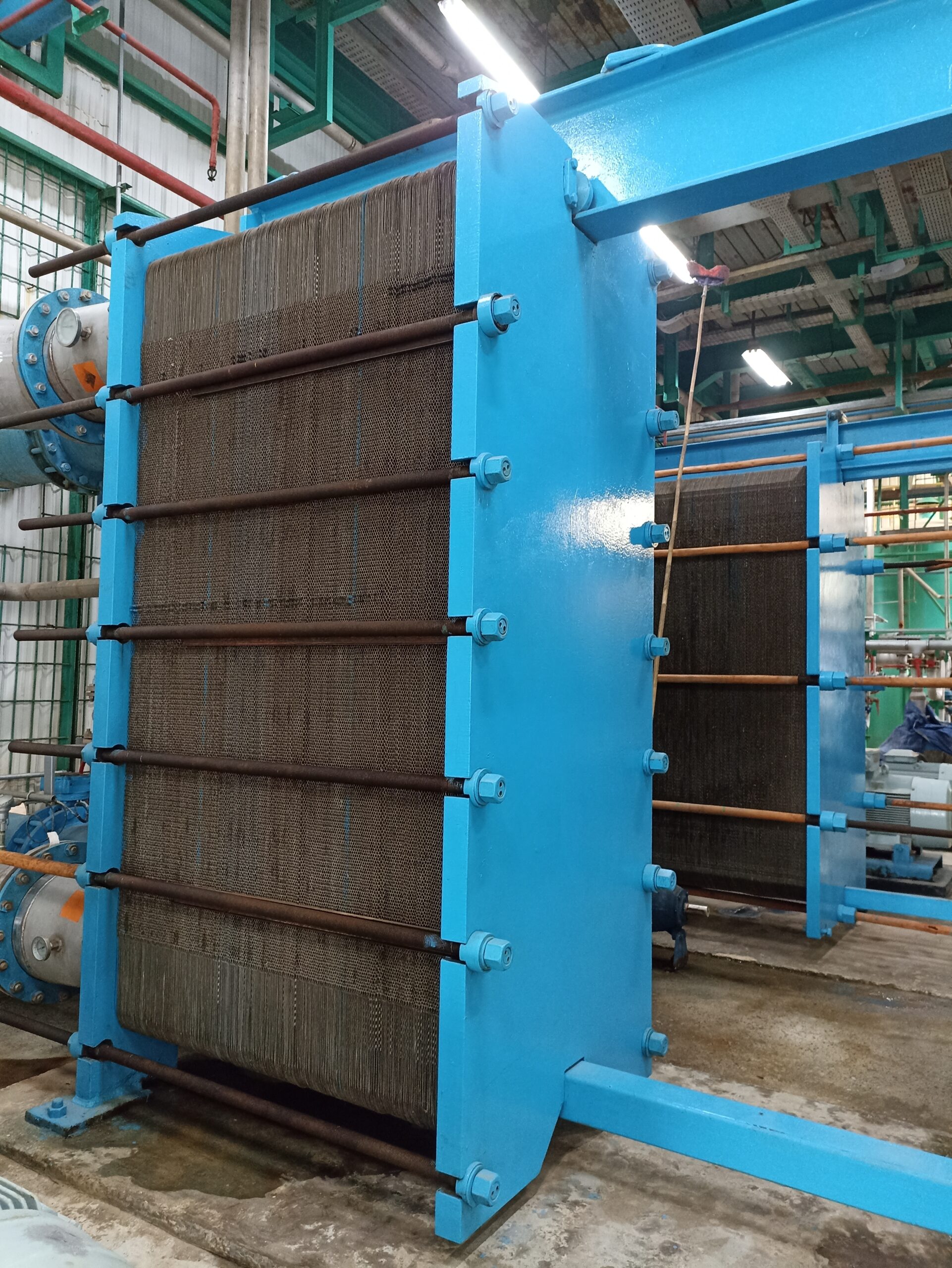
Heat exchangers play a crucial role in various industries, facilitating the transfer of heat between fluids to maintain optimum temperatures in industrial processes. With a wide array of heat exchanger options available, choosing the perfect one for your specific industrial needs can be a daunting task. In this blog, we’ll provide a comprehensive guide to help you navigate the selection process and ensure you find the ideal heat exchanger solution.
1. Assess Your Industrial Process Requirements:
Begin by understanding your specific industrial process requirements. Consider factors such as the type of fluid to be heated or cooled, the desired temperature range, flow rates, and any specific operational conditions or limitations.
2. Determine the Heat Transfer Method:
Identify the most suitable heat transfer method for your application. There are three primary methods: conduction, convection, and radiation. Each method may require a different type of heat exchanger, so it’s crucial to understand which method is most effective for your process.
3. Consider the Fluid Compatibility:
Evaluate the compatibility of the heat exchanger materials with the fluids being processed. Some fluids may have corrosive or abrasive properties that require specific material considerations, such as stainless steel, titanium, or various alloys.
4. Analyze Energy Efficiency:
Energy efficiency is a critical aspect to consider. Look for heat exchangers with high heat transfer coefficients and low pressure drops. These factors will ensure efficient heat transfer while minimizing energy consumption and operational costs.
5. Determine the Heat Exchanger Type:
Select the appropriate heat exchanger type based on your application needs. Common types include shell and tube, plate and frame, finned tube, and coil heat exchangers. Each type offers unique advantages and is suitable for specific applications.
6. Evaluate Space and Installation Requirements:
Consider the available space for installation and any spatial limitations. Some heat exchanger designs may offer more compact configurations, making them suitable for constrained spaces. Additionally, assess ease of installation and maintenance requirements.
7. Assess Maintenance and Cleaning Needs:
Take into account the maintenance and cleaning requirements of the heat exchanger. Some designs may involve more intricate cleaning procedures or require regular maintenance due to fouling or scaling issues. Opt for heat exchangers that are easy to clean and maintain, ensuring uninterrupted operations.
8. Review Industry Standards and Certifications:
Ensure the heat exchanger you choose meets industry standards and certifications. Look for certifications such as ASME, API, or ISO, which demonstrate compliance with quality and safety standards.
9. Seek Expert Advice:
Consult with an experienced industrial equipment distributor or heat exchanger manufacturer when in doubt. They can offer valuable insights and recommendations based on their expertise and industry knowledge.
10. Compare Quotes and Consider the Total Cost of Ownership:
Request quotes from reputable distributors and manufacturers, comparing prices, warranties, and after-sales services. Also, consider the total cost of ownership, including factors like energy consumption, maintenance, and lifespan, to make an informed decision.
Selecting the perfect heat exchanger for your industrial needs requires careful evaluation of your process requirements, fluid compatibility, energy efficiency, space limitations, maintenance needs, industry standards, and expert advice. By following these steps, you’ll be well-equipped to make an informed decision that ensures optimal heat transfer, efficiency, and long-term satisfaction in your industrial operations.
Contact us today to learn more. https://mullenequipment.com/contact-us/